L’impression 3D : une solution pour la production en série ?
Nous sommes début 2022, et l’impression 3D a pris une place quasi incontournable dans les phases de développement produit, et plus particulièrement pour le prototypage de produit.
Que ce soit en dépôt de fil fondu ou en frittage sélectif par laser (SLS), l’impression 3D est un moyen très efficace de passer du dessin 3D à un objet physique. Ceci va nous permettre de valider des encombrements, des assemblages, mais également des tenues mécaniques au vu de la performance de certaines technologies.
Là où il y encore 10 ans, la seule solution pour prototyper une pièce était de commander un exemplaire à son usineur préféré, attendre une quinzaine de jours (dans le meilleur des cas), et payer une note très salée… Aujourd’hui, il nous suffit d’appuyer sur “print”, et en quelques heures, nous voilà avec la pièce en mains !
L’impression 3D a révolutionné le développement de produits hardware en réduisant drastiquement les cycles d’itération. Aujourd’hui, tous les bureaux d’études disposent de leur propre imprimante 3D, chez AQ-tech nous en avons même 4, sur 2 technologies différentes.
Mais au vu de la qualité actuelle des technologies d’impression, on s’interroge de plus en plus sur la production de pièces en petite ou moyenne série.
Alors, bonne ou mauvaise idée de lancer une production en impression 3D ?
1/ Les différentes technologies d’impression 3D
Le terme impression 3D
est un terme généraliste qui désigne le procédé de fabrication par addition de matière. En d’autres termes, c’est la logique inverse de l’usinage, qui part d’un bloc de matière première et qui enlève la matière en trop pour arriver à la pièce finale.
Il existe plusieurs technologies d’impression 3D. Elles ont toutes leurs avantages et inconvénients :
Le dépôt de fil fondu (FDM)
Le dépôt de fil fondu (FDM) est sûrement la technologie la plus populaire, le principe est de partir d’une bobine de fil (généralement du PLA, ABS ou PETG) qui va passer dans une buse chauffée à 200 °C et qui sera ensuite dirigée dans trois directions X, Y et Z.
En faisant fondre le plastique, la buse va déposer à chaque passage une petite couche de plastique qui va se superposer aux précédentes (0.2mm par 0.2mm), pour ainsi obtenir la pièce en 3D.
L’avantage évident est l’accessibilité de la technologie,
pour quelques centaines d’euros, vous pouvez trouver des machines de très bonne qualité, capables d’imprimer des pièces de 20x20x20cm d’encombrement.
La qualité des surfaces est en revanche plutôt médiocre (effet strié), et la précision dimensionnelle n’est pas idéale.
C’est la technologie parfaite pour tester grossièrement une solution très rapidement et à moindre coût.
Le frittage sélectif par laser (SLS) / Multi Jet Fusion (MJF)
Le frittage sélectif par laser (SLS) et le Multi Jet Fusion (MJF) sont deux technologies très similaires. Le principe est de déposer sur un plateau une épaisseur de poudre de plastique constante (quelques microns). Ensuite, un laser vient fusionner la matière aux endroits nécessaires, travaillant couche par couche pour ainsi former la pièce.
Le MJF (HP MJF) utilise un agent liant en supplément pour avoir une meilleure tenue matière.
L’avantage de ces technologies est la qualité de l’impression, la pièce paraît légèrement granuleuse, mais cela reste très acceptable, elle peut être peinte sans problème, et la tenue mécanique est proche d’un plastique.
Il y a également toute une gamme de matériaux disponible, allant de la matière souple au plastique chargé verre !
Enfin, son prix reste raisonnable, surtout pour le MJF !
Chez AQ-tech, c’est notre technologie de référence pour prototyper les pièces plastiques lors du développement d’un produit innovant.
La stéréolithographie (SLA)
La stéréolithographie (SLA) est une technologie d’impression 3D qui polymérise de la résine par UV dans un bac de résine plein. C’est un travail qui se fait toujours couche par couche, mais beaucoup plus fin que le FDM ou le SLS, ainsi l’aspect final est quasi totalement lisse.
Mécaniquement, les pièces sont plutôt fragiles, donc cette technologie est très peu utilisable pour des validations mécaniques.
C’est un procédé assez cher, mais qui est parfait lorsqu’on souhaite développer des maquettes de présentation qui doivent avoir un aspect proche du produit final.
Une fois peint, le rendu final est assez extraordinaire, c’est la technologie que nous avons utilisée par exemple pour le prototype du casque tali-connected.
Autres
Il existe d’autres technologies comme le polyjet ou la fusion métal, mais moins utilisé, ou beaucoup plus onéreux.
2/ Pourquoi utiliser l’impression 3D pour la production ?
Toute entreprise ayant déjà industrialisé un produit sait que le hardware est très compliqué, lent et cher à mettre en production.
Une pièce plastique devra être injectée dans un moule pour être produite. Moule dont il faudra concevoir ce qui impose des contraintes importantes sur le design de la pièce (dépouilles, contre-dépouilles…).
Aujourd’hui, suivant la taille et la complexité de la pièce, un moule peut valoir entre 5000 € pour les pièces les plus petites et les plus simples, et jusqu’à des dizaines voire des centaines de milliers d’euros pour les pièces les plus encombrantes et compliquées. De plus, le temps de fabrication du moule peut varier entre 3 et 6 mois…
Plus d’informations sur notre article : comment limiter les coûts et les délais d’industrialisation d’un produit ?
Alors, lorsqu’on est une start-up et qu’on cherche à mettre rapidement un produit sur le marché, et que ce même produit va sûrement évoluer rapidement, il est naturel de ne pas vouloir se lancer dans une phase de 6 mois d’industrialisation avant d’avoir son produit sur le marché.
3/ Comment produire avec les technologies de prototypage rapide ?
La première chose à prendre en compte lorsqu’on veut produire avec l’impression 3D, c’est de s’assurer que notre pièce est compatible avec cette technologie.
En effet, si la pièce est trop volumineuse, les quantités désirées sont trop importantes ou encore les tolérances géométriques très serrées, vous allez rapidement rencontrer des problèmes de qualité.
Une fois que vous aurez validé la compatibilité de votre cahier des charges avec les solutions d’impression 3D, vient l’heure de faire le choix de la technologie à utiliser.
Pour nous, le meilleur rapport qualité, prix, délai, répétabilité est le MJF. L’aspect des pièces est très propre, bien que pas totalement lisse (légèrement granuleux), la résistance mécanique est très bonne, et enfin les prix sont très convenables.
Bien entendu, il faut être prêt à avoir une variabilité dans les dimensions géométriques de la pièce, et du rebut. Il faut donc prévoir un peu plus de quantité que nécessaire.
Pour nous, un produit qui est fabriqué en quelques dizaines d’exemplaires, et qui en termes d’encombrement tient dans la main, est parfait pour être fabriqué en MJF. C’est ce que nous avons fait pour le produit Freeside de ActivMotion.
Bien entendu, on parle ici de petites séries et aujourd’hui l’impression 3D ne peut pas rivaliser sur l’injection plastique en termes de tolérance de fabrication et de coût par pièce, mais à quel prix et délais !
Ainsi pour les produits destinés à être fabriqués en petites quantités ou amenés à évoluer rapidement, faire des pré-séries en impression 3D est vraiment une solution envisageable si on est prêt à faire quelques concessions !
+ AQ-TIPS
- Prenez le temps d’analyser la conception de votre pièce avant de choisir votre technologie d’impression. La technologie utilisée est différente selon vos besoins.
- Faites appel à un bureau d’études pour vous guider dans la production de pièces en impression 3D.
4/ Les solutions intermédiaires
On a parlé de petites pièces en petites séries. Mais qu’en est-il des plus grandes séries
, lorsqu’on veut fabriquer 100 pièces ou 1000 pièces ?
Bien entendu, si le produit est à maturité, vous pouvez basculer sur une industrialisation réelle, mais il existe tout de même des solutions intermédiaires qui permettent de garder en flexibilité et en réactivité.
Et là encore l’impression 3D facilite le travail :
Coulée sous vide
La coulée sous vide, ou duplication sous-vide, permet d’avoir des pièces proches d’une pièce injectée (en terme de rendu et de tenu mécanique) avec des coûts d’outillage très faibles.
Le principe est de faire un master correspondant à votre puis et de faire un moule en silicone autour de ce master. Ce “moule” silicone permet de dupliquer le master de façon très fidèle en coulant à l’intérieur de la résine durcissable.
Bien entendu, plus votre pièce sera compatible avec de l’injection plastique en niveau géométrique, plus le rendu sera propre, même si la souplesse du silicone permet de démouler des formes en contre-dépouille qu’un moule acier ne permet pas.
Chaque moule est utilisable pour une quinzaine de coulées, après quoi il faudra refaire un moule grâce au master.
Là ou l’impression 3D facilite grandement les choses, c’est qu’il est très facile de faire un master en SLA
, et ainsi de gagner en temps et en coûts de fabrication du master.
Injection plastique
Aujourd’hui nous trouvons des résines d’impression 3D qui supportent de très hautes températures, ce qui permet de faire des empreintes de moule d’injection en impression 3D et ainsi de réduire complètement le prix de fabrication d’un moule pour de la petite série.
Pour finir…
Vous l’avez compris, suivant votre projet, des solutions intermédiaires sont sûrement envisageables. Nous avons l’habitude chez AQ-tech de commencer par des prototypes, puis d’avancer l’industrialisation en fonction de la criticité et la complexité des pièces. Ainsi, en phase de lancement, nous pouvons très bien avoir des pièces injectées assemblées avec des pièces imprimées en MJF, des pièces en coulée sous vide et des pièces usinées ! Le tout est de bien comprendre la limite de chaque procédé.
Si vous voulez approfondir le sujet, n’hésitez pas à contacter notre équipe !
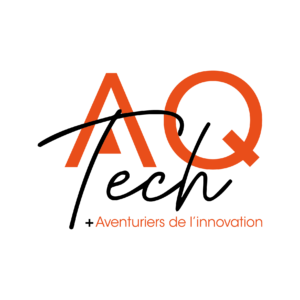
Envie d’en savoir plus sur nos aventures innovantes ?